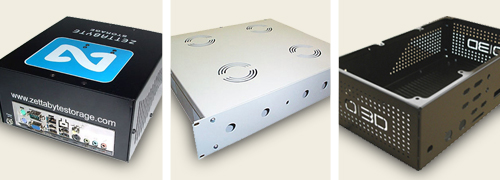
Protocase manufactures fully finished custom electronic enclosures and associated parts from a wide variety of materials and components, in 2-3 days with no minimum order. Protocase also provides expert and affordable enclosure design services.
Seam Welding
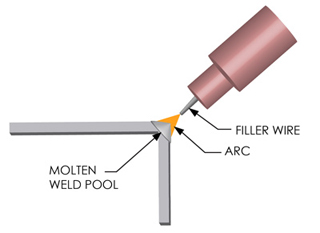
Protocase provides seam welding as a standard process. Seam welding is useful for continuously joining two or more pieces of sheet metal so that they appear seamless. To seam weld, the pieces are clamped securely and welded, and then any excess metal is removed by grinding. The resulting continuously joined seams are useful for weatherproofing, reducing EMI leakage, and for achieving a seamless look and feel when desired.
Cold Metal Transfer: Breakthrough Welding Technology
Protocase has adopted CMT welding as its standard for seam welding. CMT is a newly developed technology that far outperforms conventional TIG and MIG welding for joining light-gauge sheet metal. Before CMT, welding light-gauge sheet metal was always more of an art form than an engineered production process. MIG and TIG create excessive amounts of heat, which can cause meltback and warping, often ruining the work pieces and causing a high internal reject rate. This raised not only our internal costs but also the odds of your job being late. In contrast, CMT generates only one-tenth of the heat of MIG welding, and warping and meltback are all but eliminated. This sets new standards in welding light-gauge sheets, especially where stringent requirements exist in terms of weld-seam appearance. CMT gives you:
- Quality welds on all metal that we stock for fabrication. (Previously, we could not weld certain thin-gauge material.) For details on the metals we stock, see our pages on Cold Rolled Steel, Galvanneal, Stainless Steel, Aluminum, and copper. (copper is usually soldered)
- Lower costs, through faster weld times and reduced reject rates.
- Greater range of materials available for your enclosure designs. Whatever we can fabricate we can now weld.
How CMT Welding Works
The CMT process physically resembles wire-feed MIG welding in that a weld wire and a shielding gas are fed through a welding torch, and electricity arcs between the weld wire and the welding surface, causing the tip of the weld wire to liquefy and be applied to the welding surface. But CMT uses automatic activation and deactivation of the heating arc to systematically heat and cool the weld wire while bringing the wire into and out of contact with the weld pool many times per second. Because it uses a pulsing action instead of a continuous stream of power, CMT welding generates only one-tenth of the heat that MIG welding does. This reduction in heat is CMT's greatest benefit and is why it's called "Cold" metal transfer.
During the arcing period, the filler metal is moved towards the weld-pool. | When the filler metal dips into the weld-pool, the arc is extinguished. The welding current is lowered. | The rearward movement of the wire assists droplet detachment during the short curcuit. The short-circuit current is kept small. | The wire motion is reversed and the process begins all over again. |
![]() |
![]() |
![]() |
![]() |
Warpage and Weld Geometry in CMT Seam Welding
Corner seams (see diagram A) are geometrically stable. Stresses from temperature change and solidification are countered by the support offered by both edges of the joint. Most corner geometries can be fully seam welded without warpage using CMT welding. This is true for all metal that we stock.
T joints (see diagram B) Seams that join the edge of a part to a flat surface are prone to warping, because there is no geometric support to counter stresses from temperature and solidification of the base metal. Thus, even with CMT welding, if one makes a long seam weld across the part, it is possible that the flat surface will no longer be flat after welding. This is especially true with stainless steel and aluminum. One solution that can work in certain situations is to join by welding a number of short segments, rather than making a continuous seam. This can leave sufficient unmodified base metal to give the part enough integrity to retain flatness. If you require a T-weld geometry, our technical staff can help you with the design.
Other weld geometries need to be addressed on a case-by-case basis Contact our technical staff.
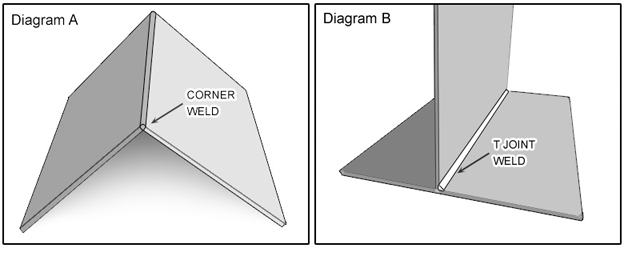